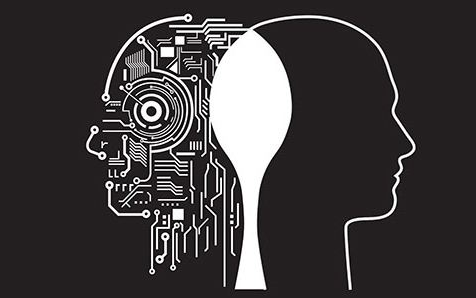
摘要: 本文剖析了传统预防维修理论的局限性,在此基础上,根据现代生产设备的故障特点,并结合我国企业设备维修管理实践,构建了现代生产设备的差异预防维修理论体系。
引言
现代生产设备技术含量高、结构复杂、系统特性强,其故障不但表现为很强的随机性,而且故障损失严重,甚至是灾难性的。
因此,对其可靠性和维修保障技术提出了更高的要求,对维修活动所涉及的无论是人员素质、维修装备、维修策略、维修计划、维修费用等相关方面都提出了严峻的考验。在这种情况下,基于浴盆曲线的传统的预防维修理论和方法已经不适应现代生产设备的维修管理,受到企业实践的严峻挑战。先进的设备亟需先进的、科学的维修理论和管理方法与之相适应。
目前国内外有代表性的维修理论有英国的设备综合工程学,美国的以可靠性为中心的维修[1-2],前苏联的计划预修制[3]和日本的全员生产维修制[4]。
上述维修理论各具特色,然而不同的维修理论有各自不同的应用环境、使用条件和文化传统背景,也有不同的优势和不足。因此,有必要针对现代生产设备的故障特点,并结合我国企业对现代生产设备的实际应用和维修管理情况,研究适用于现代生产设备的维修管理理论和方法。
1 现代生产设备的含义和故障特点
1.1 现代生产设备的含义 现代生产设备是在传统生产设备的制造技术基础上,将机械、电气、液压、自动化、计算机技术、自动控制技术等进行集成与综合,集机、电、液、气为一体的设备。现代生产设备结构复杂,技术含量高、外形尺寸大、其工作装置的容量、运转速度、加工精度、以及自动化程度和生产效率高,系统特性强。现代生产设备是我国机械工业和国民经济的重要装备,同时也是衡量一个国家工业现代化水平的重要标志。
现代生产设备的发展直接关系到国计民生的许多领域,是机械、电子、汽车、石油、化工、建筑等支柱产业和能源、交通、原材料、通讯、军工等基础产业实现现代化的重要手段。
1.2 现代生产设备的故障特点
1.2.1 随机性:现代生产设备是集机、电、液、气为一体的复杂设备,其故障的发生表现为很强的随机性,这些随机性故障不可能通过细而密的定期维修得以解决,频繁的维修不但不能改善设备的可靠性,反而易诱发更多的故障。这些随机性的突发故障给维修工作带来很大的困难与挑战。
1.2.2 复杂性:现代生产设备的故障不但表现为很强的随机性,而且故障错综复杂:故障部位可能来自于机械部分、也可能来自于电气、液压或气动部分、还可能来自于计算机控制部分;故障的原因可能是硬件故障,也可能是软件故障,还可能是人为引起的故障。
1.2.3 危害性:主要表现在故障停机损失严重。据统计,一个乙烯球罐停产一天,损失产值500万元,利润200万元,一台大型化纤设备停产1小时,损失产值80万元。现代生产设备生产效率高、工作强度大、结构比较复杂,各零部件关联又比较密切,所以往往某处微小故障就可能爆发连锁反应,导致整个设备乃至与设备有关的环境遭受灾难性的毁坏。例如:1988年英国阿尔法石油气爆炸事故;1986年欧洲莱茵河瑞士化学工业污染事故等都是设备故障造成的震惊世界的恶性事故。国内,1995年山西某电厂一台20万千瓦汽轮发电机组毁坏,直接损失达千万元[5]。
2 传统预防维修理论的局限性
我国设备维修管理从20世纪50年代起开始普遍推行前苏联的计划预修制,至今大部分国有企业仍然沿袭着这种传统的、基于时间的设备维修管理模式。然而,随着现代生产设备技术含量、结构复杂程度的增加,传统的计划预修制已明显暴露出其缺陷和弊端,主要体现在以下几个方面:
2.1 缺乏维修理论依据 计划预修制的理论基础是设备的故障特征服从经典的浴盆曲线。然而,经过60多年的发展,现代生产设备的结构、工作原理和性能都发生了很大变化,已明显不同于传统的生产设备,其故障也呈现出不同的特点,故障特征曲线有非浴盆化的趋向,并表现为多样性[6]。
2.2 维修不足和维修过剩两大问题更为突出,维修缺乏针对性。
2.3 增加设备总体故障率,降低设备寿命 计划预修理论认为预防维修工作做的越多,设备运行就越可靠,但事实并非如此。频繁的维修不但不能改善和提高设备的可靠性,减少故障的发生,反而有可能将不稳定因素带入原本稳定的系统,破坏原有的平衡状态,诱发更多的故障。
2.4 消耗大量的人力物力和财力 现代生产设备技术含量高,故障复杂,每次维修都要消耗大量的人力、物力和财力。根据电厂统计,每台200MW的机组大修一次费用平均在1000~1500万元,几乎占每台机组所创利润的30%[7]。
3 差异预防维修理论体系的构建
现代生产设备差异预防维修理论是以现代生产设备的故障特点为依据,按照设备综合管理和预防维修的思想,应用以状态维修为主的多元化维修策略,并结合我国企业对现代生产设备的维修管理实际情况,以提高设备的利用率和可靠性为主要目标的一种管理理论。
该理论的主要内容包括:对设备进行分级、分类,突出重点设备和重点部位的维修管理;对设备进行故障模式和影响分析,确定关键的故障模式;实施以状态维修方式为主、有针对性的、多元化维修策略;建立以点检和状态监测为核心的设备状态监控体系;
建立规范的设备维修管理制度;建立“三位一体”的柔性维修组织;开发并完善设备维修管理决策支持系统。
3.1 设备的分级分类管理 根据设备的重要程度将其分为A、B、C三类,即关键设备、重要设备和一般设备。
分类时主要考虑四大类十一项因素:
①可靠性因素:包括故障对人员和环境安全性的影响、故障对系统功能的影响(考虑到有无备用设备)、故障频率;
②经济性因素:包括设备重置价格、维修费用、故障引起的损失;
③生产性因素:开动班次、粗、半精加工和精加工类型、对产品质量影响;
④维修性因素:停机时间、维修难易程度。根据设备的重要性分类,采取不同的维修策略。 文/中国论文网
TPM,点检,班组建设,管理能力咨询培训@左明军老师.微信:13808969873