设备状态监控预知维修与设备全生命周期管理
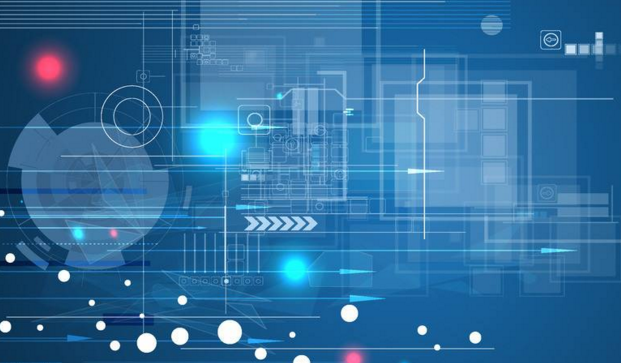
设备维修是设备整个生命周期过程不可缺少的组成部分,也是使设备在一定时间内保持其规定功能和精度的重要措施。国际上设备管理维修经历了从事后维修、预防维修到预知维修、主动维修阶段的探索,目前大多数企业都在实施多管理模式的维修,主要包括英国设备综合工程日本TPM、中国设备综合管理、健康管理等,今后的发展趋势将向预知维修转变,预知维修的基本前提是建立完善的设备状态监控体系,通过科学全面的分析准确把握设备状态,从而制定有效的预知维修策略。
1 、设备维修模式的发展现状及优缺点分析
目前设备维修模式主要包括事后维修、预防维修、预知维修、主动维修四种基本模式,其优缺点如下:
事后维修就是设备发生故障后才进行的非计划维修,即发生事故时立即停机修理,又称故障维修。其优点是不必在状态监测上投资、不会出现过度维修,缺点是无法预测事故停机、存在设备二次损坏及生产损失、管理失控的风险。
预防维修就是根据设备磨损的统计规律或经验,事先确定检修类别、周期、内容,定期进行停机维修。优点是维修以可控制的方式在方便的时间进行、减少意外事故,有效避免灾难性事故、可更好的控制备件、节约资金,缺点是状态良好的设备也被频繁检修(维修过剩)、仍存在计划外故障停机。
预知维修是以设备状态监测为基础,根据设备日常检查、定期重点检查、在线状态监测和故障诊断所提供的信息,经过分析处理,按设备实际状态来决定维修时间与内容。优点是可减少意外停机、减少备件储备、只需在适当时候进行维修,缺点是监测成本较高。
主动维修就是以故障根源分析为基础,基于可靠性的维护,为了消除设备的先天性缺陷或频发故障,对设备的局部结构或零件的设计加以改进,并结合检修过程实施的检修方式。优点是设备寿命延长、可靠性增加、减少故障及二次损坏、停机时间减少、总维护费用降低,缺点是监测成本较高、人员技能及分析要求较高。
2 、设备状态监控策略研究与探讨
设备状态监控,也就是通常意义上的设备点检。是为了提高、维持设备的原有性能,通过人的五感(视、听、嗅、味、触)或借助工具、仪器,按照预先设定的周期和方法,对设备上规定的部位进行有无异常的预防性周密检查,以使设备的隐患或缺陷能够得到早期发现、早期预防、早期处理。设备状态监控的要素主要包括震动、磨损、泄露、异音、松弛、龟裂、油脂、压力、温度、流量等。
目前,国外的状态监控已由原来的低水平、局部的状态监控阶段,进入由计算机管理的具有监测、判断、警告等功能的高级阶段,实现了对状态的适时、全面、准确的评价,设备状态监控体系已经是一个包含信息化平台、设备点检、设备状态信息收集、分析、判断、维修计划制定、维修行为及维修后验收、考核、激励等内容的完整体系,设备的操作、维修点检人员等通过检查、检测等手段,收集、分析和处理设备技术状态变化的信息,及早发现或预测设备的功能失效和故障,适时地采取维修或更换等对策,以保证设备处于良好的技术状态。
长期以来,我们行业曾普遍实行的是以事后维修、预防性计划检修为主的检修体制。通过研究其他行业设备状态监控的开展情况,结合行业设备特点,我们的经验是以设备点检为抓手,将传统点检方法和精密点检仪器(如:振动、红外、超声波等)紧密结合,结合计算机、网络通讯、数据库与设备状态监测和故障诊断技术,构建日常点检、专业点检、精密点检相结合的三级点检体系,并依托设备信息化管理系统,为设备预知性维修提供可靠的数据依据,逐步实现设备状态可控及精益化管理。
一是策划现代化的设备状态监控管理体系。根据企业设备特点搭建设备点检防护体系,确定管理职责和状态监控人员的地位,形成设备状态监控与维修相互制约、相互支撑的关系,落实“八定”点检体系,即定人、定法、定标、定期、定点、定项目、定点检表格、定记录。同时对设备进行分类,确定一般监控设备和重点监控设备,选取无冗余、故障高发、大功率旋转、高发热量配电、高价值类设备作为重点监控设备。
二是培养专职设备点检人员。选取具有超前设备管理意识、一定设备维修年限和丰富维修经验、较全面扎实的理论基础、较强的设备状态分析能力、较强的学习能力、协调能力、熟悉设备的工作原理、性能、设备发生故障的原因、检修方法和改进措施的人员担任专职点检人员。通过长时间的分析积累,形成设备故障曲线库,为设备预测性维修提供数据依据。
三是建立标准化设备监控操作规范。结合行业设备的特点进行定点、定标,标准的设定应以设备生产厂家的技术资料、ISO标准、国家标准或行业标准、设备长期运行所积累的经验数据、同类机型状态数据等为参考依据;日常点检标准以开机条件、产品工艺参数为主;专业点检标准以保障设备完好、稳定运行的设备性能指标为主;精密点检标准以能够反映设备性能劣化程度或劣化趋势的定量参数为主(定量参数通常为振值、温度、电流、速度、压力等),并通过持续的积累经验,不断完善优化标准。
四是落实三级点检责任。日常点检主要由操作工通过感官,对设备开机和运行条件类因素进行点检;专业点检主要由维修工通过感官、借助监测工具,对设备关键部位进行专业点检,分为机械专业和电气点检;专职精密点检由专职点检员借助仪器,定期对设备关键部位进行点检,并对三级点检产生的异常信息,利用长期积累的数据、图形、图像进行审核、分析、筛选,提出维修建议,对维修结果进行跟踪验证,同时根据点检及维修结果的相互比对,对点检标准进行持续优化。
五是运用信息化技术进行自动诊断及系统分析。随着信息化、网络技术的迅速发展,为设备状态监控的开展提供了强大的支撑。在现有的设备管理信息系统中增加设备状态监控内容,借助信息化技术手段来实现定性、定量监测数据的收集、整理、分析与应用,使设备状态监控工作逐步实现系统化、流程化、智能化,为设备预知性维修提供支撑,为三级状态监控人员的业绩考核提供依据,促使设备状态监控标准的持续优化及设备状态监控水平的不断提升。
总之,工厂设备状态监控是一项系统性和探索性的工作,需要结合实际情况不断进行研究和改进,初步提高设备精益化管理水平。
1 、设备维修模式的发展现状及优缺点分析
目前设备维修模式主要包括事后维修、预防维修、预知维修、主动维修四种基本模式,其优缺点如下:
事后维修就是设备发生故障后才进行的非计划维修,即发生事故时立即停机修理,又称故障维修。其优点是不必在状态监测上投资、不会出现过度维修,缺点是无法预测事故停机、存在设备二次损坏及生产损失、管理失控的风险。
预防维修就是根据设备磨损的统计规律或经验,事先确定检修类别、周期、内容,定期进行停机维修。优点是维修以可控制的方式在方便的时间进行、减少意外事故,有效避免灾难性事故、可更好的控制备件、节约资金,缺点是状态良好的设备也被频繁检修(维修过剩)、仍存在计划外故障停机。
预知维修是以设备状态监测为基础,根据设备日常检查、定期重点检查、在线状态监测和故障诊断所提供的信息,经过分析处理,按设备实际状态来决定维修时间与内容。优点是可减少意外停机、减少备件储备、只需在适当时候进行维修,缺点是监测成本较高。
主动维修就是以故障根源分析为基础,基于可靠性的维护,为了消除设备的先天性缺陷或频发故障,对设备的局部结构或零件的设计加以改进,并结合检修过程实施的检修方式。优点是设备寿命延长、可靠性增加、减少故障及二次损坏、停机时间减少、总维护费用降低,缺点是监测成本较高、人员技能及分析要求较高。
2 、设备状态监控策略研究与探讨
设备状态监控,也就是通常意义上的设备点检。是为了提高、维持设备的原有性能,通过人的五感(视、听、嗅、味、触)或借助工具、仪器,按照预先设定的周期和方法,对设备上规定的部位进行有无异常的预防性周密检查,以使设备的隐患或缺陷能够得到早期发现、早期预防、早期处理。设备状态监控的要素主要包括震动、磨损、泄露、异音、松弛、龟裂、油脂、压力、温度、流量等。
目前,国外的状态监控已由原来的低水平、局部的状态监控阶段,进入由计算机管理的具有监测、判断、警告等功能的高级阶段,实现了对状态的适时、全面、准确的评价,设备状态监控体系已经是一个包含信息化平台、设备点检、设备状态信息收集、分析、判断、维修计划制定、维修行为及维修后验收、考核、激励等内容的完整体系,设备的操作、维修点检人员等通过检查、检测等手段,收集、分析和处理设备技术状态变化的信息,及早发现或预测设备的功能失效和故障,适时地采取维修或更换等对策,以保证设备处于良好的技术状态。
长期以来,我们行业曾普遍实行的是以事后维修、预防性计划检修为主的检修体制。通过研究其他行业设备状态监控的开展情况,结合行业设备特点,我们的经验是以设备点检为抓手,将传统点检方法和精密点检仪器(如:振动、红外、超声波等)紧密结合,结合计算机、网络通讯、数据库与设备状态监测和故障诊断技术,构建日常点检、专业点检、精密点检相结合的三级点检体系,并依托设备信息化管理系统,为设备预知性维修提供可靠的数据依据,逐步实现设备状态可控及精益化管理。
一是策划现代化的设备状态监控管理体系。根据企业设备特点搭建设备点检防护体系,确定管理职责和状态监控人员的地位,形成设备状态监控与维修相互制约、相互支撑的关系,落实“八定”点检体系,即定人、定法、定标、定期、定点、定项目、定点检表格、定记录。同时对设备进行分类,确定一般监控设备和重点监控设备,选取无冗余、故障高发、大功率旋转、高发热量配电、高价值类设备作为重点监控设备。
二是培养专职设备点检人员。选取具有超前设备管理意识、一定设备维修年限和丰富维修经验、较全面扎实的理论基础、较强的设备状态分析能力、较强的学习能力、协调能力、熟悉设备的工作原理、性能、设备发生故障的原因、检修方法和改进措施的人员担任专职点检人员。通过长时间的分析积累,形成设备故障曲线库,为设备预测性维修提供数据依据。
三是建立标准化设备监控操作规范。结合行业设备的特点进行定点、定标,标准的设定应以设备生产厂家的技术资料、ISO标准、国家标准或行业标准、设备长期运行所积累的经验数据、同类机型状态数据等为参考依据;日常点检标准以开机条件、产品工艺参数为主;专业点检标准以保障设备完好、稳定运行的设备性能指标为主;精密点检标准以能够反映设备性能劣化程度或劣化趋势的定量参数为主(定量参数通常为振值、温度、电流、速度、压力等),并通过持续的积累经验,不断完善优化标准。
四是落实三级点检责任。日常点检主要由操作工通过感官,对设备开机和运行条件类因素进行点检;专业点检主要由维修工通过感官、借助监测工具,对设备关键部位进行专业点检,分为机械专业和电气点检;专职精密点检由专职点检员借助仪器,定期对设备关键部位进行点检,并对三级点检产生的异常信息,利用长期积累的数据、图形、图像进行审核、分析、筛选,提出维修建议,对维修结果进行跟踪验证,同时根据点检及维修结果的相互比对,对点检标准进行持续优化。
五是运用信息化技术进行自动诊断及系统分析。随着信息化、网络技术的迅速发展,为设备状态监控的开展提供了强大的支撑。在现有的设备管理信息系统中增加设备状态监控内容,借助信息化技术手段来实现定性、定量监测数据的收集、整理、分析与应用,使设备状态监控工作逐步实现系统化、流程化、智能化,为设备预知性维修提供支撑,为三级状态监控人员的业绩考核提供依据,促使设备状态监控标准的持续优化及设备状态监控水平的不断提升。
总之,工厂设备状态监控是一项系统性和探索性的工作,需要结合实际情况不断进行研究和改进,初步提高设备精益化管理水平。
TPM,点检,班组建设,管理能力咨询培训@左明军老师.微信:13808969873