精益体系适用工具的灵活应用
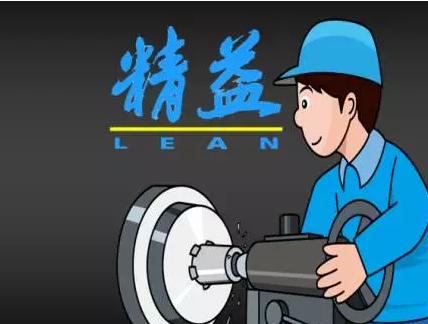
一、支持5S的工具
1、一个流生产:
就是将作业场地、人员、设备合理配置,使产品在生产时每工序只有一个在制品或成品,从生产开始到完成之前没有在制品放置场地及入箱包装作业。须生产线专业化布局。
2、VSM价值流:
是一种用来描述自客户始到客户终的信息流、工艺流及物流的工具。目的是为了识别和减少供应链整个过程的浪费。应用程序:现状图;计算现有节拍、平衡率及查找瓶颈,识别不良/资源和作业(程序及动作工时等)浪费;用IE工具进行改善;未来流程图。
3、拉动式计划系统:
生产计划部门只制定主生产计划,采购、车间/工段根据主生产计划按下游车间/工段的需要及采购/制造周期来制定采购和生产计划。
日生产指令按照生产前置周期提前由最后一道工段/工序发出,通过“看板”逐级向前工段/工序传递,依此实现适时适量按需生产。
二、现场不良和浪费对5S的影响:
1、库存过多:数量失控,容易混淆,现场凌乱;导致不必要搬运、堆积、防护、寻找等动作和时间浪费;
2、设备排列不合理:增加搬运距离,无效作业多,半成品数量大;
3、设备保养不良:故障率高,品质难保证,打乱现场秩序;
4、存货摆放混乱:增加寻找时间,先进先出困难、易呆滞、变形、变质;
5、工装杂乱放置:增加寻找时间、无效走动时间;场所秩序混乱;
6、通道不明或被占:物流不顺,增加搬运时间;对人和物易造成损害;
7、工作场所脏污:影响品质,易发生装备/品质/安全等方面事故。
三、持5S的四化:
1、柔性化:设计开发部门通过模块化产品设计、柔性的工艺设计、设备/工装适用范围柔性化实现多品种通过的生产线柔性化;
2、均衡化:向前工序/工段均匀地领取各品种,各品种按日混合生产,多品种切换,工作日之间日生产品种/产量均衡,工人忙闲均衡;
3、准时化:综合平衡配送料、零件加工、总成装配品种数量及时间段,准时领发料,准时生产交货,实现适物、适量、适时的生产准时化;
4、生产同步化:
(1)要求从采购到生产到发货各个阶段、环节及物流的运动完全与市场需求同步;
(2)工序/工段/车间之间不设中间库存,零件加工、总成组装、性能检测平行进行,成批生产;
(3)品种之间通过尽量缩短作业切换时间缩小生产批量,工序之间通过平衡单件节拍达成单位时间产量同步,工段之间通过建立细胞生产线平衡不同工段的生产节拍达成生产同步;
(4)整个流程的生产同步化通过“后工序/工段领取、前工序/工段按需生产”的拉动式生产系统实现,后工序只在需要的时候到前工序领取所需品,前工序只按后工序要领走的品种、数量和时间进行生产。逐序、逐工段、逐部门拉动直到材料采购部门、到供应商,整体联动实现生产、采购业务同步化。
四、持5S的看板系统及标识系统:
1、生产看板:
看板,是传送指令、信息、信号的工具,它可以是某种板、牌、卡片、流程卡标识卡等表单等形式,也有彩色兵乓球、空容器、地面空格提示、信号灯开关提示灯等形式。
作用是:a生产或采购运送、搬送的作业指令;b防止过量过早生产或搬送;C生产信息目视化。
2、标识系统要求:
(1)标识必须形象生动,直观易解,应采用人/物品/自然物的鲜明特征、标牌/实物标样/图片/照片等形式,作到一目了然。标识载体物必须美观醒目,经久耐用。规格一致化,同类标识内容及载体结构标准化;
(2)由企管和品管部门牵头公司环境标识标准化活动,确定标识应用方位、标识办法、设计维护部门;
(3)基础IE适用工具:
一、工程分析改善法:
1、加工:有没有可有可无的工程和可以同时进行的工程?有无加工时间多的工程?能否提高设备的能力?能否跟其他的工程一起进行?改变工程的顺序能否取得改善效果?现有的产量多少,是否适当?
2、搬运:
a.能否减少搬运的次数?能否增大单次搬运数或重量减少搬运次数?能否对工程进行合并,减少搬运次数?
b.能否缩短搬运距离?
d.能否改变作业场所布置以便减少或取消搬运工作?
e.装、卸货工作是否耗费很多时间?能否缩短?
3、停滞:
a.能否减少停滞的时间,提高周转率?
b.能否通过工程的剔除、合并、重排、简化来消除停滞?
c.生产线工序工时及产能是否平衡?可否再提高平衡率?
二、标准工时及线平衡:
1、标准工时:是熟练程度达标的操作工人,在严格遵守规定的设备器具、作业及检验程序/动作、工艺参数等工艺纪律及相同作业环境情况下,生产一件合格产品所耗费的时间(工序单件作业时间T单),并作为执行及考核的定额标准;
2、 线平衡:即生产线各工序工时及产能平衡的程度;
(1)线平衡的意义:通过计算线平衡率及平衡损失率,衡量生产线各工序工时及产能平衡程度,寻找平衡率及系统产能提升的潜力,以取得生产线最佳投入产出效率;
(2)线平衡计算公式:a.线平衡率=各工序工时之和/瓶颈工序工时x工序数量
X100%;平衡损失率=1-线平衡率;b.最佳的平衡率要兼顾产能规划、投资能力、产品生命 周期及投资回收期等因素确定,取得最佳匹配。
标准作业:
将通过先进原理工具确定的工序工步作业程序、动作、生产装备、工艺参数、标准工时通过标准作业文件固化下来,作为作业及目标控制的标准依据,实现最佳作业资源配置及绩效输出目的。
搬运及布局优化:
1、制订或优化成最优搬运方案:
(1)综合考虑搬运对象搬运强度连续性周期性搬运场所等特点选择搬运手段及设备器具、搬运成本;
(2)搬运动作优化消除拿取次数及反复作业,人和产品防错完好防护。
2、制订或优化成工厂最优布局方案:
(1)基于最佳工艺流程工艺资源配置;
(2)基于先进的对象专业化及流线型或单元U型线的生产线布局;
(3)基于最佳程序动作物流绩效要求。
3、输出最优物流绩效:最优的搬运投入产出比;最少搬运距离及时间;最低物流成本。
4、布局及物流设计原则:
(1)工厂总布局及物流设计
①按照产品实现的工艺及物流顺序,依次布置材料准备、加工、处理、部件/总成装配车间(工段)位置,且距离较近,衔接紧密;
②尽可能让材料进场到成品入库之间各环节在流程中同步不停顿进行,避免或减少中间在制品、零配件及料箱占用生产面积,减少流动资金占用,保证物流效率,以实现拉动式、一个流、浪费少的精益生产方式;
③以生产车间(工段)位置为基准,布置材料库、配件库、工具库、成品库等,与生产车间(工段)距离适中,保证领取或入库距离最短,效率高;
④水电气动力/环保/安全健康等生产辅助设施围绕生产单位配套布置,距离适当。
(2)生产车间工段内部布局设计:
①生产线设置,根据厂房结构及空间特点、生产方式对直线型或U型生产线进行选择,形成一个流先进生产方式。同时,物流仓储设施匹配配置;
②水电气动力供应做好规划并围绕使用点配置。环保/安全/保健措施、人文等辅助设施配套配置;
③生产线之间、设备之间距离要满足物流效率要求,通道宽度适宜,方便现场清扫,噪音密度不超标,操作者无压抑感;
④车间工段宏观布局协调,整齐美观,物流路线畅通、距离最短。在此前提下充分使用厂房面积,提高单位面积产量/产值率。
定置管理原理和要求:
1、定置管理原理:
a.根据工艺需要,确定现场应存在物品种类及数量;
b.根据与人结合的紧密程度不同将物品ABCD分类进行不同标识,确定存放位置及与人的距离,查找迅速,保证工作效率;
c.及时清理废弃物,创造舒心的工作环境。
2、定置设计要求:
a.定置设计必须确保物品处于合适的位置、距离、状态,使操作者取放感到顺手快捷,无障碍;
b.根据生产量及频率确定被加工物存放区域及区域大小,确定合格品区、待检区、返修品区、废品区、待处理品区等检验区域位置、物品转运起点区、待清理物品暂存区等位置。各区域实行颜色区分;
c.根据与工作/操作者/生产车间/转运器具或物流设备结合的紧密频度,确定工作/生产区/仓库各物品A、B、C类别,选择适宜的距离及定置点。定置点最好有定点区划或行迹指引;
3、现场定置要求:
现场物品摆放通过定置图进行科学规范控制,大件/重物靠外,码放高度安全、不超高,摆放距离适宜,防止磕碰,储存器具适宜,物品数量受控,所有物品摆放整齐,美观;通道线、区域线清晰明确,区域标识、大类别标识、分类标识、细分类标识、名称/数量/时间标识等物品标识和检验状态标识清晰、完整。
TPM,点检,班组建设,管理能力咨询培训@左明军老师.微信:13808969873